
Why need data-driven industry to sustain in 4IR era
Abrar H Sayem | Wednesday, 24 November 2021
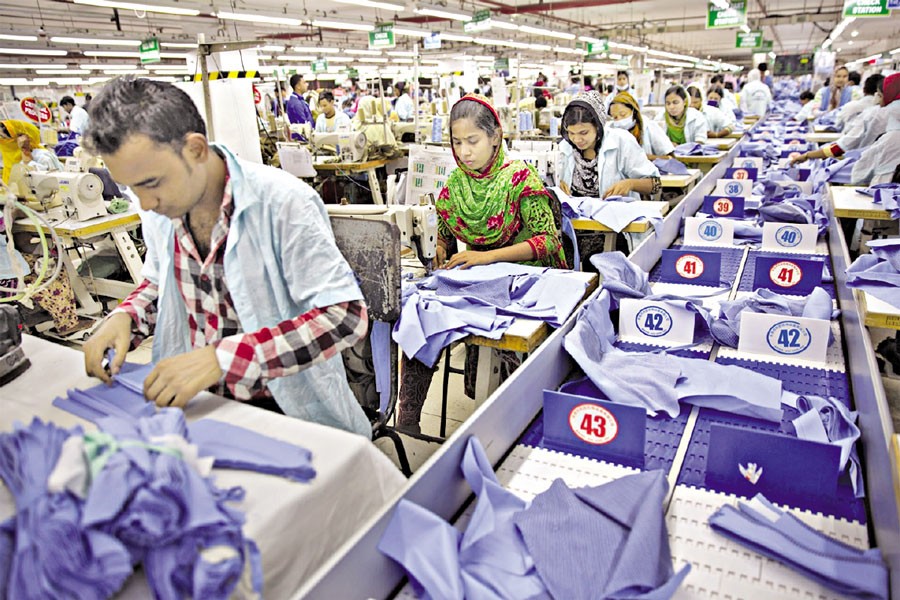
The world is going through the fourth industrial revolution, which is a fusion of advances in artificial intelligence (AI), robotics, the Internet of Things (IoT), 3D printing, genetic engineering, quantum computing, and other latest technologies. That is a big leap of technology adaption in today's world. The pace of technology growth has never been faster. Adaptation remains the moot question, for sheer sustenance of a nation's progress so far attained.
According to a survey by McKinsey, companies expect this end-to-end digital integration -- from raw material all the way to the final product delivery -- to yield a productivity improvement of as much as 26 per cent. Now in contrast -- here is the largest export-earning industry of Bangladesh, which is also the second-largest RMG manufacturer of the world -- we are still lagging with the adoption of the third industrial revolution, automation. Positive side is, compared to the 3rd industrial revolution, the 4th revolution will have relatively high impact at comparatively little replacement of equipment, which shows a way of catching up fast.
While we have increased efficiency with many advanced automated types of machinery, we are still far behind in increasing our operational efficiency and the major reason behind this is the lack of digitisation. Digitisation means to convert something into a digital format, and usually refers to the encoding of data and documents. The importance and significance of data in our manufacturing business are still under a shadow. The result of this is our below-average operational efficiency compared to our top global competitors.
Operational efficiency is closely related to productivity. While our productivity is steadily growing still the pace is significantly less than our other competitors like India and Sri Lanka. According to Bangladesh Productivity Masterplan 2010-15, Bangladesh achieved 4.61-per cent productivity growth, while in the same time Sri Lanka and India's growth were 5.21 per cent and 5.41 per cent respectively. As productivity is closely related to national GDP, business and individual efficiency, it's time we explored all the options that could help us achieve faster growth. I believe data intelligence has a big role to play to help us get there.
The ready-made garment or RMG industry generates a huge amount of data every day, data of daily production, types of defects, incoming and outgoing raw materials etc. All these data could have been clear indicators of factory performance, which would let the management take more data-driven decisions, as well as could make the organisation more process-driven. Not only in the RMG industry but in every industry is it applicable that if our operations could be analysed with business-intelligence tools, then monitoring and managing would have been much easier and it would lead to increased efficiency.
Without the right set of analysed data, it is always difficult to go into the root cause of any problem, hence sometimes the solution to a problem does not lead to the most optimised one. After the covid-19 setback, now that businesses started running again, cost optimisation to maximise profit and balance the losses is the core agenda of businesses, but with the influx of orders, now if there is an increased operational expense more than forecast or somewhere production is not meeting the planned outcome, it becomes really difficult and time-consuming for management to address the core reasons behind it. Often it tends to address the problem as it comes reactively. Even then the improvement and its level of effectiveness get difficult to measure.
Whereas, with the right set of analysed data helps us run business in a proactive manner. With insights from past and real-time data, a manufacturer can have benefits like reduced downtime, improved productivity, better capacity utilisation, more accurate forecasting, higher flexibility, streamlined production processes, and improved efficiency. Ultimately, the business will see a significant increase in profits by using data analytics to help them make the important decisions about their day-to-day operations.
For example, the maintenance contract that Siemens has with various British rail operators regarding their Desiro UK trains is an example of such a situation. Siemens uses data from continuous monitoring and predictive maintenance to guarantee 99-percent train availability. This results in increasing customer satisfaction for UK rail operators, while generating additional revenues for Siemens. This new approach to data opens up additional value for businesses and such models can replicate in RMG manufacturing, too. Manufacturers, for this, just have to get the fear out and think progressively.
Through identifying ways to significantly optimise operations, data analytics will predictably raise profits. There was research outlined in a Capgemini white paper which shows that operational improvement can increase profits up to $117 billion globally, compared to customer analytics which 'only' creates $38 billion. But we see retailers investing heavily in acquiring customer analytics to maximise the profit whereas the manufacturers are lagging in capitalising on this opportunity.
In manufacturing industry, top-and mid-level managers can use advanced analytics to take a deep dive into historical process data, identify patterns and relationships among discrete process steps and inputs, and then optimise the factors that prove to have the greatest effect on yield. Many global manufacturers in a range of manufacturing industries and geographies now have an abundance of real-time shop-floor data and the capability to conduct such sophisticated statistical assessments. They are taking previously isolated data sets, aggregating them, and analysing them to reveal important insights. A recent McKinsey survey of manufacturing and supply-chain professionals found that 93 percent plan to focus on resilience of their supply chain, and 90 percent plan to invest in talent for digitisation. For example, digital performance management (DPM) has been a popular early-use case at a wide range of companies, including several small precision-engineering companies where pilots of DPM have helped boost productivity by 40 to 70 percent. We are still stuck in pen and paper or at most spreadsheets.
The first step to becoming this data-powered organisation is to implement a culture and system for collecting all sorts of data in digital format. It works as the hub of information from which different areas of a business can be analysed and monitored for their efficiency. Communications between departments can also be improved by using one system.
Data-driven industry is what the rising economy of Bangladesh needs to make more strategically aligned decisions and take calculative risks. Decisions from cutting costs to streamlining and expanding operations are all highly needed to be backed by past data for a profitable and sustainable business future of the country.
The writer is the president of Bangladesh Apparel Youth Leaders Association (BAYLA), managing director of Merchant Bay Ltd and director at Sayem Group.
sayem@merchantbay.com